In this issue’s Mario on Maintenance column Mario Kuisis deals with risk management and suggests that, as we slowly return to normal business practices following several years of unpredictability, plant and industrial operators should look beyond survival and towards reducing operational uncertainty to minimum levels possible.
For many South African businesses, if not most, the main focus of the past year or two has been about survival in an uncertain economic and political environment. There has therefore necessarily been great attention devoted to cost reduction. We have discussed many examples of how proactive maintenance can make a great contribution here. However, as indications of a return to normal business strengthen, it is time to start examining some other business fundamentals that were relegated to a back seat. One of the more important of these is organisational risk management.
Whilst concentrating on assuring survival, other business risks have not gone away. If anything, many have increased. So let’s take a look at how, in particular, proactive maintenance can make a useful contribution to managing organisational risk in asset intensive organisations.
By definition, risk is the effect of uncertainty on business objectives. All organisations have a natural aversion to risk as it renders the future unpredictable and therefore more difficult to manage. Trust and confidence of all stakeholders is enhanced when the degree of uncertainty is contained to acceptable levels, at reasonable cost.
The radically revised and recently published ISO 31000 Risk Management standard sets out excellent guidelines for organisational risk management. It is intended for those people who create and protect value in organisations. The general approach is to apply a set of basic principles in a structured framework that is coordinated with a defined process. The relationship between these is detailed in the standard and illustrated diagrammatically by the figures opposite.
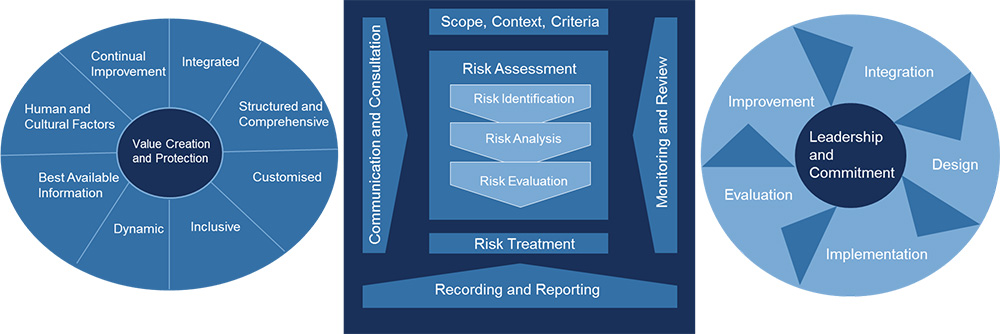
There are of course different types of risk that an organisation must consider (strategic, compliance, operational, financial, reputational, etc). There are also a host of potential origins, both external and internal and including environmental, human and cultural influences. Some examples are natural disasters, health and safety incidents associated with products or services used or supplied, influence of industrial action in and outside the organisation, security threats, raw material and utility supply interruptions, OEM support for key production equipment, adverse market trends, economic headwinds, legislative policy changes, etc. Most of these risks are not pertinent to this discussion. Our interest is wherever physical assets come into the picture, as this is where value can often be found by applying the principles of proactive maintenance.
Note we are not talking about typical operational reliability issues. Nor is it about Risk Based Maintenance (RBM). That is a perfectly valid proactive maintenance approach, but for these purposes that is considered to be a part of normal business and having an impact on the cost of doing normal business. It is not the subject of this discussion. We are dealing with matters of governance and leadership at the top level of the organisation.
Our concern here is with the materialisation of an incident, situation or event that may be in isolation, trigger a cascade or be a catalyst to others that individually or together threaten organisational objectives or sustainability or possibly even survival. The risk may be in the form of a sudden safety incident, environmental disaster or mission critical asset failure. In the case of physical assets the impact on the organisation is typically in the form of extended business interruptions affecting all or major parts of the organisation. It may also be a more insidious situation. For example, where critical assets are unknowingly deteriorating faster than projected, with consequent inadequate financial provision for timeous capital replacement.
When it comes to risk assessment, the team needs to identify and describe existing threats and emerging risks with relevant, current and accurate information that also clearly conveys limitations of knowledge, reliability of data and time related influences.
As is evident from the principles, top management is responsible for ensuring that risk is properly and effectively managed. This would be translated into a policy that defines needs and expectations, responsibility and authority. Practically, execution relies on persons with the requisite skills, experience and resources to oversee risk management and give effect to the policy. Inclusivity requires that engineering and maintenance teams take care of risks in their sphere of the organisation. They will be expected to demonstrate leadership and commitment by ensuring that risks are properly considered and understood, with systems implemented to effectively manage the risk. Remnant risk must be appropriate and there must be clear communication of the risks and their management.
When it comes to risk assessment, the team needs to identify and describe existing threats and emerging risks with relevant, current and accurate information that also clearly conveys limitations of knowledge, reliability of data and time related influences. Factors to consider for meaningful risk analyses include likelihood of the event, consequences in nature and magnitude, complexity, stability and influence of time, effectiveness and confidence level associated with existing controls.
Clearly this is a difficult requirement at the best of times, but even more so when the stakes are high. Many of these tasks rely on information and insights that are hard to come by. This is where the principles of condition assessment and condition monitoring can make a meaningful difference.
Guesswork, subjective judgement based on visual inspections, empirical evidence and hearsay can be replaced with objective data. The fact that this option exists may not be obvious to those concerned with risk management, as they will not necessarily be exposed to the techniques and technologies that will be evident to those who work with them on a routine basis. The aim of this discussion is to promote awareness and encourage internal dissemination of knowledge for the application of non-destructive testing, condition assessment and condition monitoring beyond the realm of routine maintenance.
Examples include silo, flue-gas stack, bridge, reservoir, dam wall, cooling tower, pipeline, power boiler and other civil structures. The likes of mills, fans, pumps, compressors, turbines, conveyor lines, valves, pipe networks, pressure and storage vessels are generally well covered by predictive maintenance – and statutory inspection and tests in some instances – which ensures that most risks are well covered. However, if any of these are mission critical in a single stream process then it is essential to conduct a more in-depth risk analysis to consider potential abnormal modes of failure and consequences.
Similarly, in the electrical world it may be transmission lines, pylons, poles, power transformers, high voltage cables, generators, motors or switchgear. Much can be achieved with periodic assessments that are not possible or practical on a routine basis to look for evidence of slow developing but catastrophic failure modes.
Most importantly, routine methods may be insufficient for some of the assets and failure modes. Experts may need to be called in periodically to conduct assessments employing specialist technologies to gain insight where it is not possible to do so otherwise. In this way the task of organisational risk management can be rendered simpler, more effective and more reliable to the benefit of all stakeholders. In the case of physical assets it enables the guideline requirements of ISO 31000 to be applied fully and properly.
Interestingly, many insurance underwriters who provide cover for the burden of remnant risk will recognise the benefits of such proactive measures through reduced premiums. The simultaneous reduction of organisational risk and operating expenditure makes this an attractive option for any leading business.
I suggest this is certainly worth consideration in the normal business environment that we are all looking forward to.