What is maintenance readiness?
Assets fit for purpose and ready to maintain at project handover – encapsulating the importance of the maintenance readiness within the greater operational readiness landscape.
We can define operational readiness as the required conditions and staffing under which a new or existing facility can function in a stable and sustainable way to achieve its intended output. Without an Operational Readiness process, assets will be operated and maintained with unnecessary waste, leading to higher life cycle costs. Examples include inappropriate operation, inadequate approach to maintenance, lack of supply support and an inability to consistently drive continuous improvement.
The focus of maintenance readiness is on the maintenance and reliability-related activities within the operational readiness landscape. Maintenance readiness includes the processes and activities required to ensure that enterprise assets are designed fit for purpose and are ready to maintain at project handover. It ensures that the site team can take ownership of the assets and can perform maintenance on the assets safely, efficiently, and in a sustainable and environmentally friendly manner. This approach enables the site team to manage the assets for all of the assets’ operational life. The process will not only benefit the current team on site but also the people who will need to operate and maintain the equipment in the future.
The impact of maintenance readiness on an asset’s life cycle
The value of operational readiness and its sub-set of maintenance readiness in an asset’s life cycle should not be underestimated. The application of the maintenance readiness process and commitment by all stakeholders in the early stages of the process can have a vast impact on asset life cycle costing. This is well illustrated in the graph below.
Value and ROI on maintenance readiness
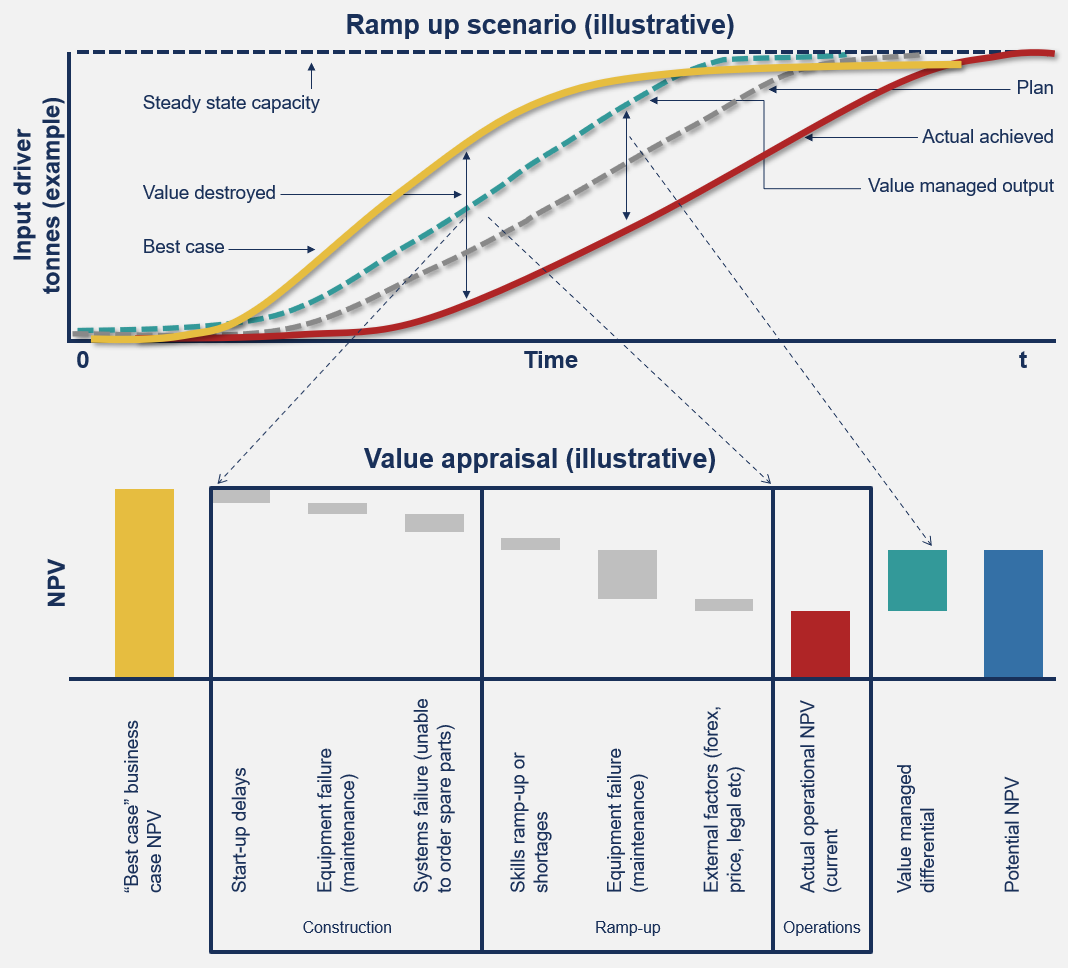
The maintenance readiness process is usually initiated by the Project team applying rigorous focus to the detailed technical design and build aspects of the project. If this is neglected from the outset, it can potentially lead to practical challenges in achieving the desired return on investment at project close out. It is suggested that the transition from execution to operations is where high-value leakage occurs.
Certain case studies illustrated that up to 30% of the initial study value has been destroyed. (Illustrated in the graph alongside.) [Source: Adapted from Deloitte, 2012. Effective Operational Readiness of Large Mining Capital Projects – Avoiding value leakage in the transition from project execution into operations. Article.]
A framework for maintenance readiness
The maintenance-related activities that make up an operational readiness plan for a site are typically set out in a maintenance readiness framework. The framework takes a systems approach to address the interrelated nature of the processes and activities. It is up to the project’s team in consultation with the site’s operations to decide which aspects of maintenance readiness are brought into their project. For example, they may agree to leave out key activities, owing to the maturity of existing site processes, or competencies of site teams. Identified elements should be integrated into the overall operational readiness plan.
The maintenance readiness process can be applied in part or in full to:
- Greenfield establishments, for example new factories, power plants and airports are built from scratch on greenfield land.
- Brownfield extensions, for example a pre-existing site or facility, which is modified or upgraded to launch a new production activity.
- Procurement of a new major piece of equipment.
- Extensive rehabilitation of a major process or facility.
The positive impact of involving Operations early in the process
Alignment between the Design, Operations and Maintenance departments will ensure an investment performs at the desired level from the beginning.
The site and project teams should establish an agreement as part of the commissioning plan that describes in detail the project handover and acceptance criteria. This will ensure that both teams are aligned and will work towards the same target. The involvement of the operational team from an early stage in the project will ensure a smooth handover of the investment.
The role of the reliability engineer
The involvement of reliability engineers is a key success factor for maintenance readiness projects. They typically perform the following activities during a project:
- Develop RBD diagrams and RAMS analyses
- Participate in the development of criteria for an evaluation of equipment suppliers, MRO suppliers, and technical service providers.
- Develop acceptance tests and inspection criteria as part of the commissioning plans.
- Coordinate QA/QC during manufacturing, transport, storage, installation and commissioning stages.
- Perform defect elimination investigations for critical assets.
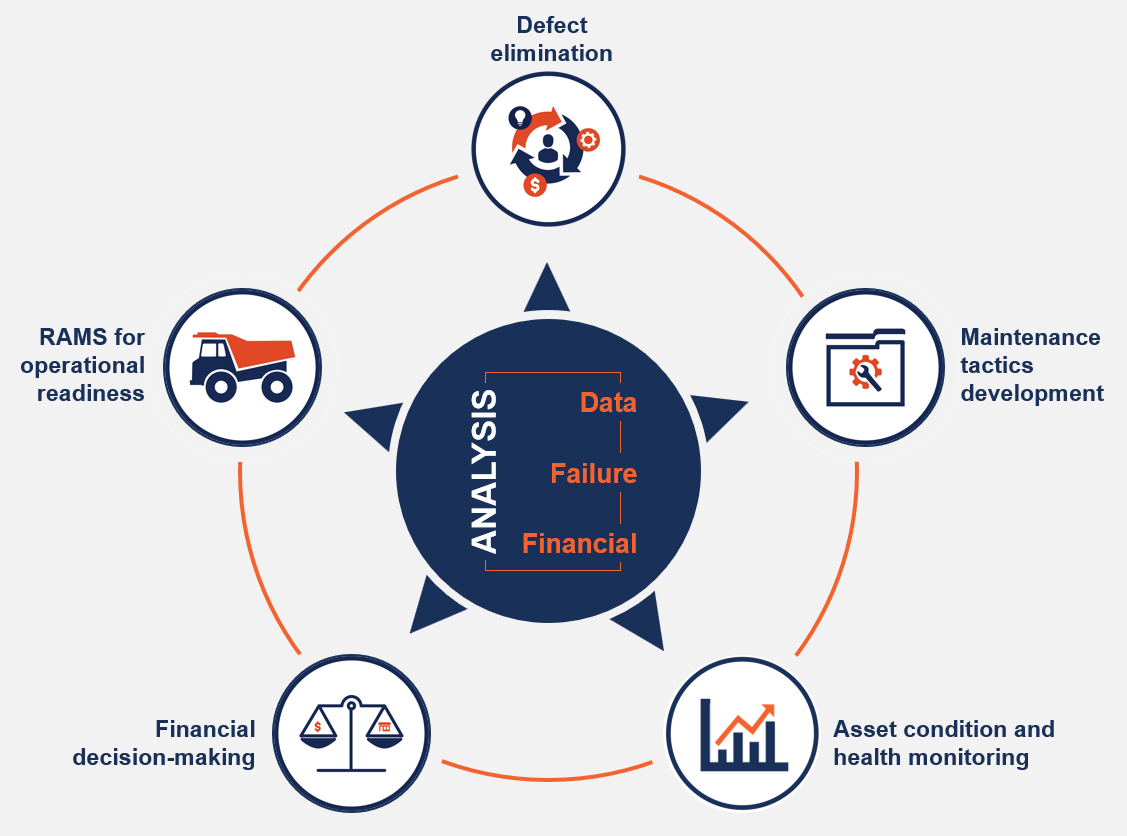
Pragma has developed dedicated role definitions for reliability engineers and we offer specialist RE training courses in support of their roles.
Typical maintenance readiness activities performed during a project life cycle
Most asset-related projects are managed through a stage-gate process, with typical stages listed in the infographic below.
The maintenance readiness framework functions in a similar way to a generic project plan where we assist in meeting the client’s requirements. We provide support as they progress through each review stage of the project.
Pragma has customised a generic project model through which it achieves maintenance readiness for specific client needs as is described in the stages and activities below.
Pragma Maintenance Readiness Project Model
At this stage, the client will still be evaluating a variety of opportunities to produce a robust business case. Therefore, our involvement is limited to providing the client with estimates of what the typical maintenance readiness activities are, and the effort entailed to reach them should the project proceed to the pre-feasibility stage. This will enable the client to enter the next stage with a clear plan and budget provision for completing the required maintenance readiness work during pre-feasibility.
We can provide the most value for our clients if we are on board from the pre-feasibility phase. This is where the reliability specifications are documented, based on the asset strategies and the detailed design determined from the initial notational designs. The intent of the pre-feasibility phase is to define the investment details for the selected alternative and confirm the business case. The end result is that the client is provided with:
- Maintenance readiness plan and budget for Feasibility
- Maintenance readiness team proposal for Feasibility
- Draft EAMS plan
- Tested reliability specification for the project
- Preliminary details for critical assets
- Maintenance support requirements
Once the business case has been defined and agreed upon, this is refined in the feasibility phase. RBD diagrams are refined, and further RAMS and RAMBO analysis is also carried out if required. The end result is that the client is provided with:
- Updated maintenance readiness plan and budget for Execution
- Detailed Maintenance team (considering outsourcing decisions)
- Document Management systems for maintenance readiness deliverables and a detailed EAMS plan
- Reliability and maintainability analysis to influence the final design
- Detailed specifications in support of the procurement packages for critical equipment
- Detailed asset tactics development plan to be implemented during the Execution stage
- Plans to deliver maintenance facilities, tools and spare parts
- Any life cycle costing calculations to clarify asset selection
- Design the performance measures and tools for critical equipment
During Build and Deliver, most of the plans developed during feasibility need to be executed. This includes:
- Develop the detailed functional location structure and asset register
- Develop all the maintenance tactics and populate the chosen EAMS
- Deliver the training plans for the new team, or finalise agreements with outsourced service providers
- Identify, code and procure all of the maintenance spare parts, and establish the initial stock parameters
By the time the project reaches Commissioning, the maintenance management and reliability management functions are in place for operating the new assets. They will have the responsibility to build on this foundation and also drive the long-term asset management plan.
The site and project teams should establish an agreement as part of the commissioning plan, that describes in detail the project handover and acceptance criteria. This will ensure that both teams are aligned and will work towards the same target. The involvement of the operational team from an early stage in the project will ensure a smooth handover of the investment.
In the end, it all comes down to operating the investment to achieve the business case. Here we can assist with:
- Conduct RCAs on problem areas
- Facilitate the Post Mortem of the project and document the lessons learned
- Ensure final documentation, asset registers, maintenance plans and spare parts are updated to ‘as-built’ status
A holistic approach to maintenance readiness
Capital projects need to be completed on time and on budget and also be ready to operate as envisioned within the investment business case.
Project success should not be measured by performance against budget and schedule alone, but also by the timely achievement of the designed production levels. Maintenance readiness focuses attention on the activities which need to be planned and implemented to transition the facilities, plants and assets to an operating business. This will achieve the approved business case objectives and specific project deliverables.
Despite the inherent complexities and effort required to attain maintenance readiness, and ensure a smooth transition from project to operations – success is possible with the right maintenance readiness team.