Why do we say ‘Mine the gap’?
At the recent Joburg Indaba, Mametja Moshe, Pragma Chairperson, hosted hosted a crucial session where she and her panel dissected the topic, “Capital allocation, cost containment and operational efficiency: are mining companies investing in their future?” We believe that smart maintenance investments are the key to bridging today’s disruptions and tomorrow’s success. Strategic maintenance drives reliability, availability, and profitability in mining operations by optimising capital allocation and ensuring cost containment.
This is where Pragma comes in. We are perfectly positioned to close the gap between the current state of asset management at most mining houses and optimal asset performance. We are also perfectly positioned to help mining houses embrace the power of positive disruption in enterprise asset management and help the mining industry move forward.
Asset management in the mining industry
The mining industry faces complex maintenance challenges, essential for safe and cost-effective operations. Asset management is crucial from the planning stages of a new mine to its operation, influencing equipment availability and reliability. Although external factors affect mining, managers can control the condition and availability of equipment. Advancements in technology and digitalisation enhance forecasting, control, and reporting, aiding in predictive maintenance and reliability engineering, which are key to reducing downtime and extending equipment life. Despite these advancements, many mines still experience frequent equipment breakdowns, environmental incidents, and low staff morale. Leveraging our extensive experience, we offer solutions to these pervasive maintenance challenges in mining.
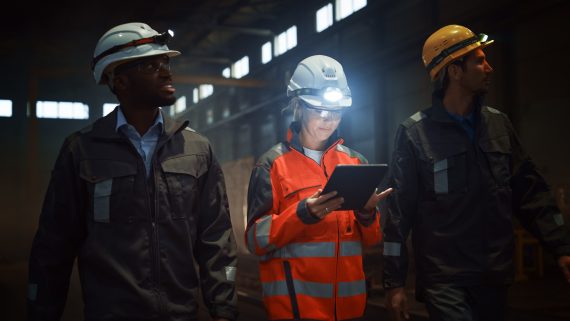
Compliance saves lives
The mining industry faces extensive legal compliance requirements due to high accident risks and potential loss of life, production, and environmental damage. Stringent maintenance practices are crucial for equipment safety. Accurate reporting of maintenance tasks is vital to avoid disciplinary charges or legal action.
Mining houses rely on internal resources and contractors, emphasising the importance of agreed standards and procedures. Effective enterprise asset management systems (EAMS) and work management apps, like the On Key Field Engineering app, facilitate planning, management, and enforcement of maintenance work.
Asset risk management involves everyone in the business, and Pragma’s approach includes training and a functional framework. Unskilled resources play a significant role in accidents, highlighting the need for practical maintenance courses to comply with regulations and mitigate risks.
Technical skills save time and money
Due to stricter legislation and advancing mining processes and equipment, mining companies require competent technical staff. Qualified planners, schedulers, artisans, and business intelligence engineers must oversee maintenance activities without project delays or downtime. Automation and technology require programmers and data analysts with a deep understanding of maintenance and asset management.
Pragma offers resourcing benefits, providing skilled resources for advisory projects and long-term asset care service contracts. Our Academy trains learners in asset management, offering recommended learning pathways for role-specific skills and aiding in succession planning for clients.
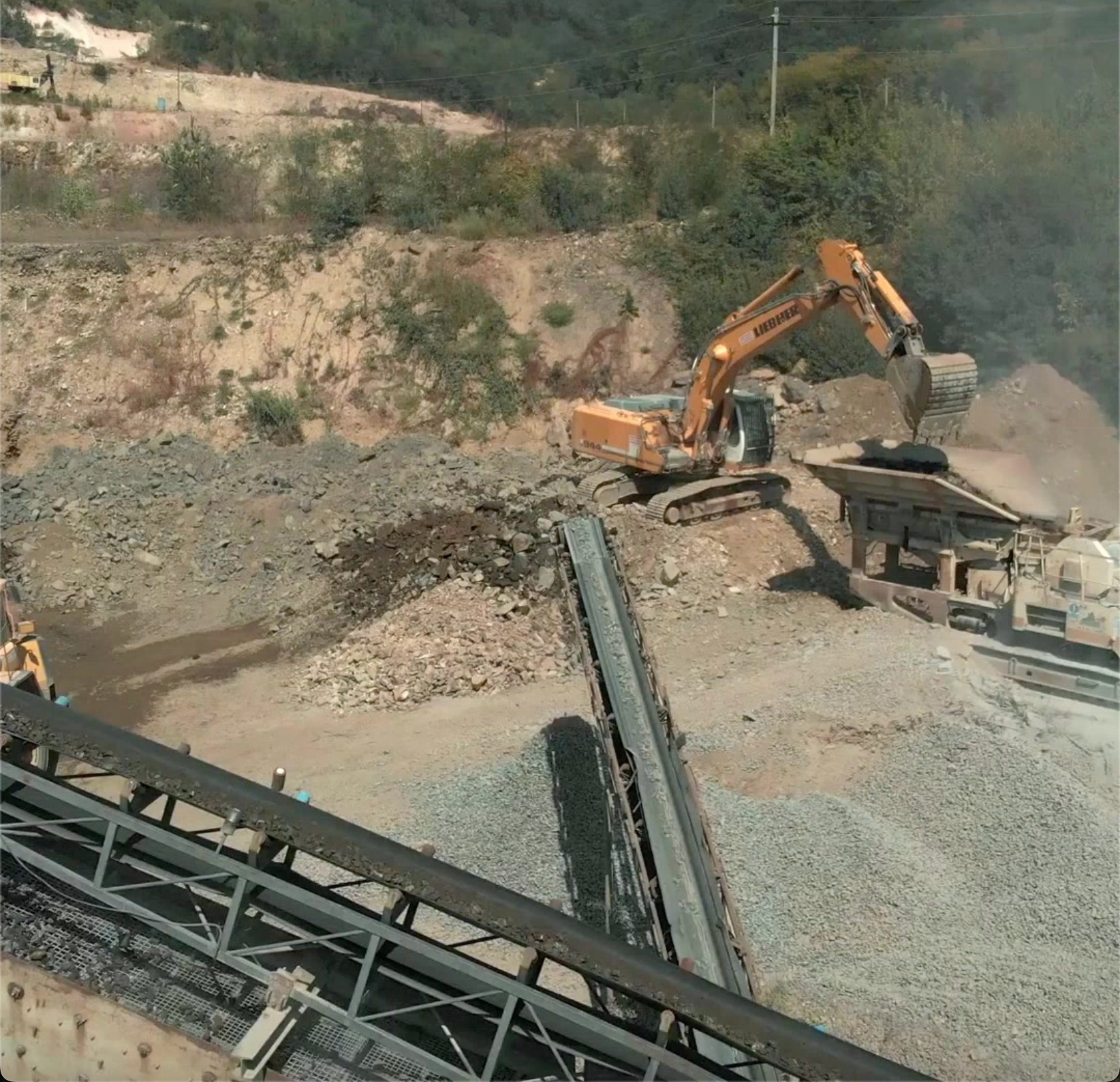
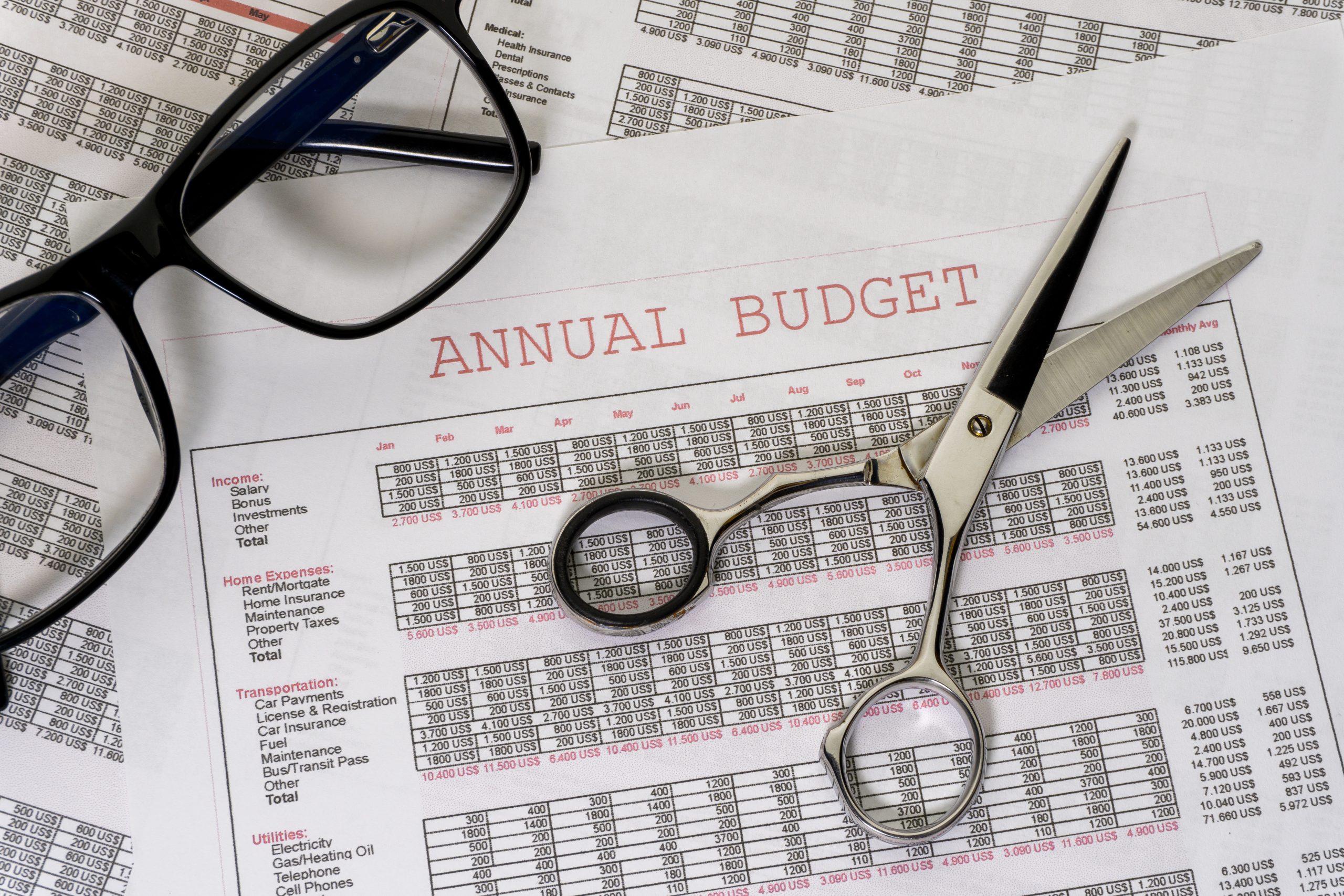
Stretching maintenance budgets
Mining companies face the challenge of managing costs with declining maintenance budgets, leading to neglected maintenance and frequent breakdowns. Decreased budgets result in lower productivity, revenue, safety hazards, and environmental incidents. To optimise budget spending:
- Prioritise critical equipment maintenance and postpone non-essential tasks using a criticality analysis and risk assessment.
- Implement cost-saving measures like predictive maintenance and extending equipment life through repair.
- Utilise condition monitoring and IoT technologies for better failure visibility and budget planning.
- Understand equipment life span and associated maintenance costs using life cycle costing.
- Standardise equipment types, manage spare parts, and reduce maintenance skills required for efficiency.
Standardise maintenance processes for more efficiency
Standardising maintenance processes in mining improves safety, efficiency, and equipment maintenance. Ways to achieve this include developing preventive maintenance programs, implementing computerised maintenance management systems (CMMS) like On Key, establishing standard operating procedures (SOPs), and fostering a culture of continuous improvement. Pragma’s solutions, such as asset health monitoring using IoT technologies and mobile work management applications, support these efforts. Standardisation ensures consistent and correct work execution, reduces errors, and enables effective management of maintenance plans and resources. Regular evaluation and improvement enhance overall performance and safety. Standardising maintenance processes control costs, improve equipment reliability, and ensures compliance with mining safety and environmental regulations.
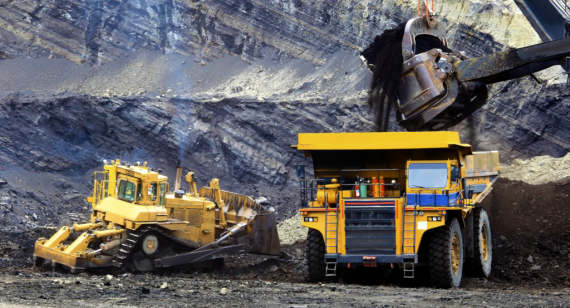
Reliability engineering, the answer to frequent breakdowns and extended downtime
Investing in a reliability engineering programme is crucial for mining houses struggling with equipment failures. It focuses on critical assets and optimising their performance to prevent future failures. This proactive approach reduces downtime and maintenance costs. Reliability engineering in mining involves identifying failure modes, developing preventive maintenance plans, implementing reliability-centred maintenance (RCM), using condition monitoring techniques, establishing performance metrics, conducting root cause analysis, and implementing predictive maintenance techniques. Pragma offers reliability engineering solutions, including full-time engineers, consultation, coaching, and learning pathways to empower mining teams to manage and execute reliability engineering programs.
Collaboration between maintenance, engineering and supply chain
Maintenance, engineering, and supply chain integration and communication are vital for efficient mining operations. To achieve this, implementing an inventory management system, a computerised maintenance management system (CMMS), and regular communication processes between teams are essential. Similarly, integrating with the store department optimises material flow and availability. Implementing an enterprise resource planning (ERP) system, establishing communication channels, and developing a supplier management program are effective strategies. These measures enhance equipment uptime, reduce maintenance costs, and improve safety by ensuring prompt parts availability and swiftly addressing issues.
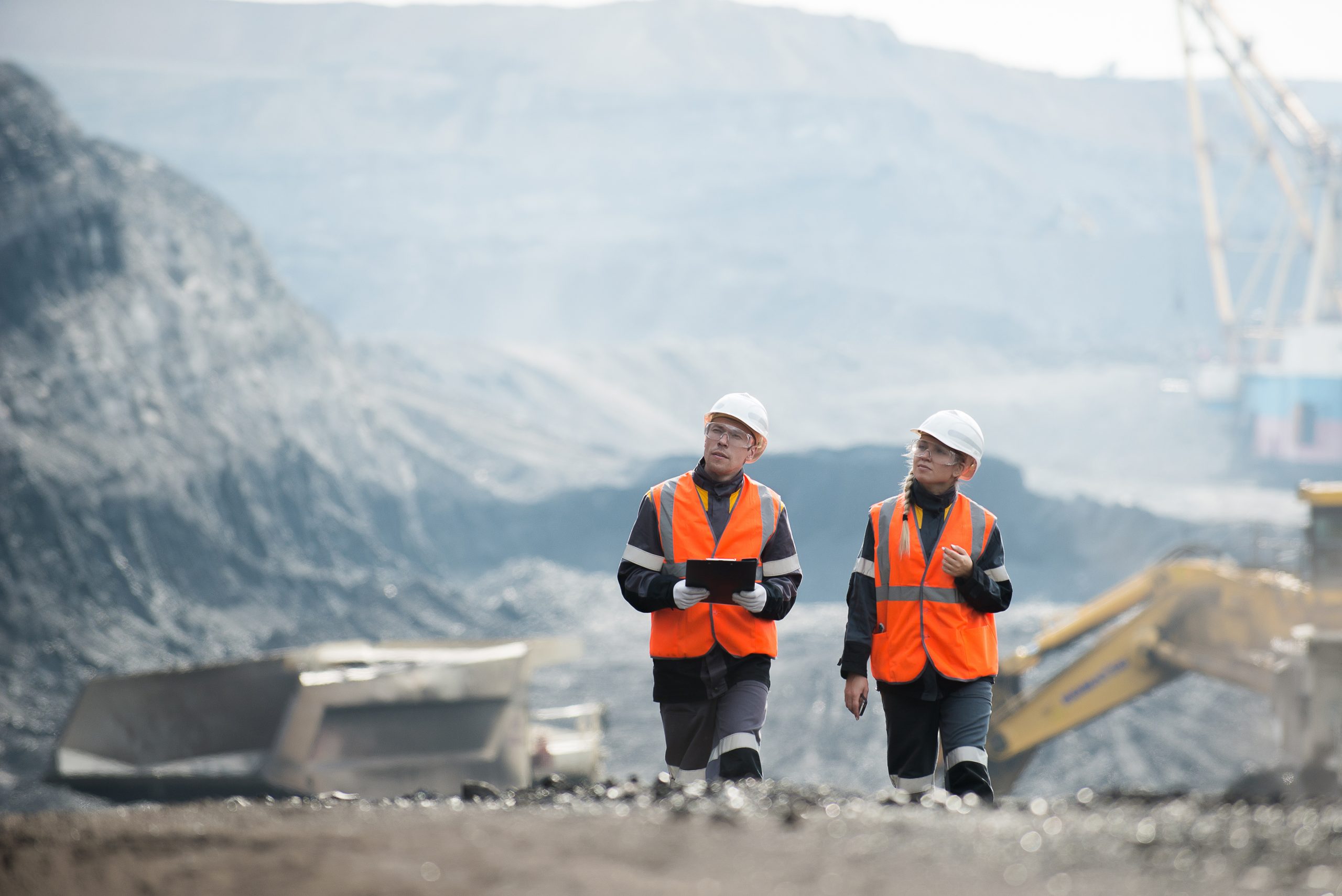
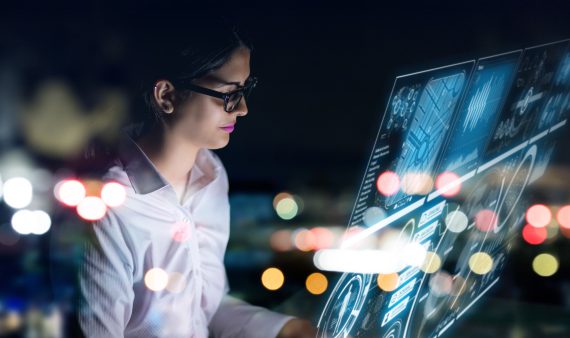
Master data management
Master data management (MDM) is crucial in mining to address various challenges caused by the lack of accurate data. MDM involves collecting, consolidating, and maintaining accurate data about critical assets, enabling informed decision-making. It includes identifying and classifying critical data, validating and storing data in a central repository, ensuring accuracy and consistency, implementing data governance, and utilising data analytics. An effective MDM system improves maintenance efficiency, enhances equipment performance and reliability through predictive maintenance, ensures regulatory compliance, and reduces costs. MDM is essential for mining companies to effectively manage and utilise data from mining operations and maintenance activities.