Arveen Gobind of Martec, a Pragma Group company, describes how IIoT technology is now being used in condition-based maintenance programmes to extend the lives of transformers and other critical plant equipment.
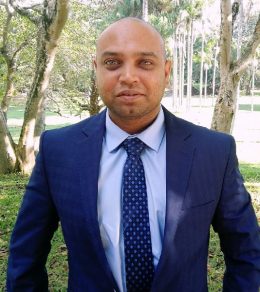
Living in the present time in South Africa where the economy is not at its best, all areas of public and private sectors are forced to tighten their collective belts on capital expenditure. This financial constraint is the result of the cascaded effect of reductions in monthly spend, which is leading industry to venture into extending asset life and to promote sustainability by implementing condition-based maintenance principles.
Hospitals, data centres, communication infrastructure facilities and heavy industries alike are critically dependent on a reliable electric power supply. Power and distribution transformers form an integral part of operational sustainability, either by servicing a production line or to supply residential networks.
A large packaging company was experiencing problems related to high moisture content and moderate dissolved gas analysis (DGA) gas production rates on some of its most critical transformers. These transformers are identified for replacement in the year 2020, but the client wanted to monitor these units, as a failure would pose significant risk on the sustainability of operations. A proactive decision was made to eradicate this problem by implementing a condition-based maintenance programme facilitated by an automatic and efficient in-time transformer monitoring system.
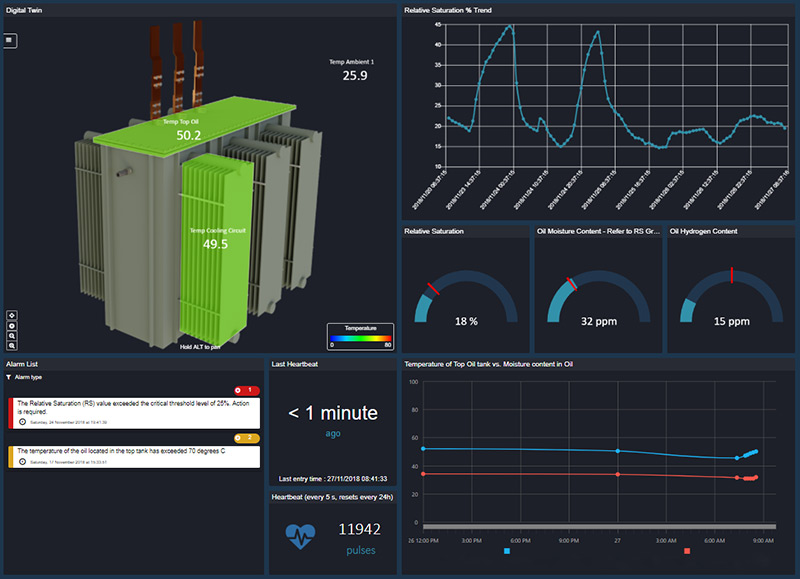
An effective protection system, complemented by monitoring and diagnostics of transformers, are the most important techniques for extending the life of a transformer. Based on the transformer failure statistics, the failure location analysis and previous oil analysis data, the insight to the transformer winding condition was derived as most valuable for an indicative health status.
An effective monitoring and diagnostics system are able to process transformer fundamentals, acquire, process and store data, and derive corrective actions based on inputs, setpoints, alarms and algorithms.
A system was installed based on an IIoT system designed to continuously monitor moisture and dissolved hydrogen in transformer oil, utilising on-line DGA technology for local and remote monitoring with predictive analytics. Furthermore, winding and oil temperatures, relative saturation and load are measured for correlation and analytics. This system continuously monitors the transformer in real-time and compares sensor outputs from the transformer with the reference values of a healthy transformer.
Adapting to industry 4.0, an IIoT-based transformer monitoring system for power transformers has been designed, implemented and tested. A Cloud based application that is linked to an IIoT gateway via Ethernet is installed in this system to timeously receive and store transformer data in an accessible database. After experiencing deviations from setpoints or any abnormality, immediate action can be taken to prevent any catastrophic failures of power transformers.
A trigger initiates an SMS notification expressing the alarm condition raised. The monitoring system details may be accessed via any Internet connection with given authorisation.
The successes gained through the implementation of the transformer health monitoring system, provide operational advice on the loading of the transformer. Trends revealed heavy loading of the aged transformers in short durations, which triggered relative saturation alarms.
The monitoring of moisture and oil temperature also permits planning for off-line dry-outs. The transformer DGA results are stable and there is some low-level gasing, which is indicative of low-level overheating under operational conditions.
The monitoring technique allowed the condition risk levels to be assigned with confidence. This allows better prioritisation of those transformers that require the most urgent maintenance.
Condition monitoring with predictive algorithms has an important role for a reliable electrical supply, preventing unplanned outages and promoting reliability.
This article first appeared in the November 2018 edition of MechChem Africa.