Digital transformation is high on the agenda of many companies across the world and all industries. The manufacturing industry has been flooded with IoT and digitalisation-based content, including videos, webinars and articles. The solutions often seem too advanced and very pricey.
IoT is not new to the industry, but its use is growing in intensity, probably because IoT promises to make manufacturers’ lives easier. Yet, the following questions often come up:
- What is digital transformation?
- What are the trends and technology available to us now?
- How does it affect our people?
Undoubtedly, early and successful adopters of new technologies often gain advantages that enable them to establish new ground in the industry before the technology becomes more widely used. But, before we get ahead of ourselves, let us get a reality check to understand what the end game is all about. What is digital transformation?
Since digital transformation will look different for every company, it is hard to pinpoint a definition. Simply put, digital transformation is the process of combining digital technologies into business operations to change the way business functions fundamentally. It is also about finding new opportunities in an existing business to redesigning how value is delivered to the business and its clients. For example, digital transformation allows companies to design asset maintenance processes in a much more efficient way. As the digital transformation advances within companies, all areas of operations are affected, including maintenance management.
Technology trends
The manufacturing industry has always relied upon the use of technology. In the past, manufacturers would schedule routine maintenance on equipment to find any unnoticed malfunctions, which resulted in halted production and cost money. Today, maintenance influences all aspects of business, including efficiency and risk, safety, the environment, energy efficiency, costs, product quality and customer service.
With the investment in digital technology, machines are developed with internal sensors that send messages to notify workers when maintenance is required. With a real-time alert and response system, predictive maintenance technology catches mechanical failures even before they happen.
Traditionally, the objective was to find the optimum frequency for replacing components to minimise the overall costs. Figure one shows the probability and costs of breakdowns vs the cost of preventing failures by pro-actively replacing components.
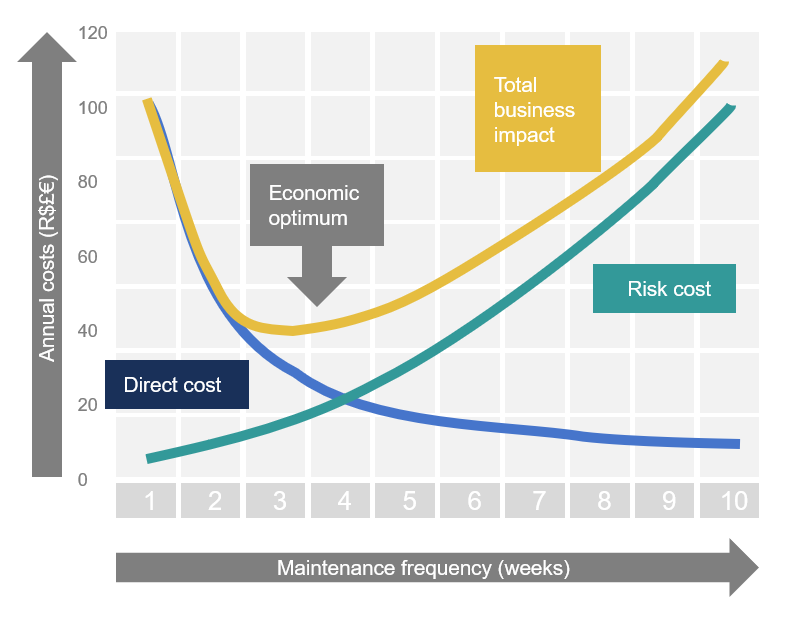
Back in 2020, researchers from Verdantix identified the trends in technology roadmaps for asset management technologies and compiled a helpful graphic to illustrate the value and associated growth of these technologies (Verdantix, Global Corporate Survey 2020: Operational Excellence Budgets, Priorities & Tech Preferences, 22nd December 2020).
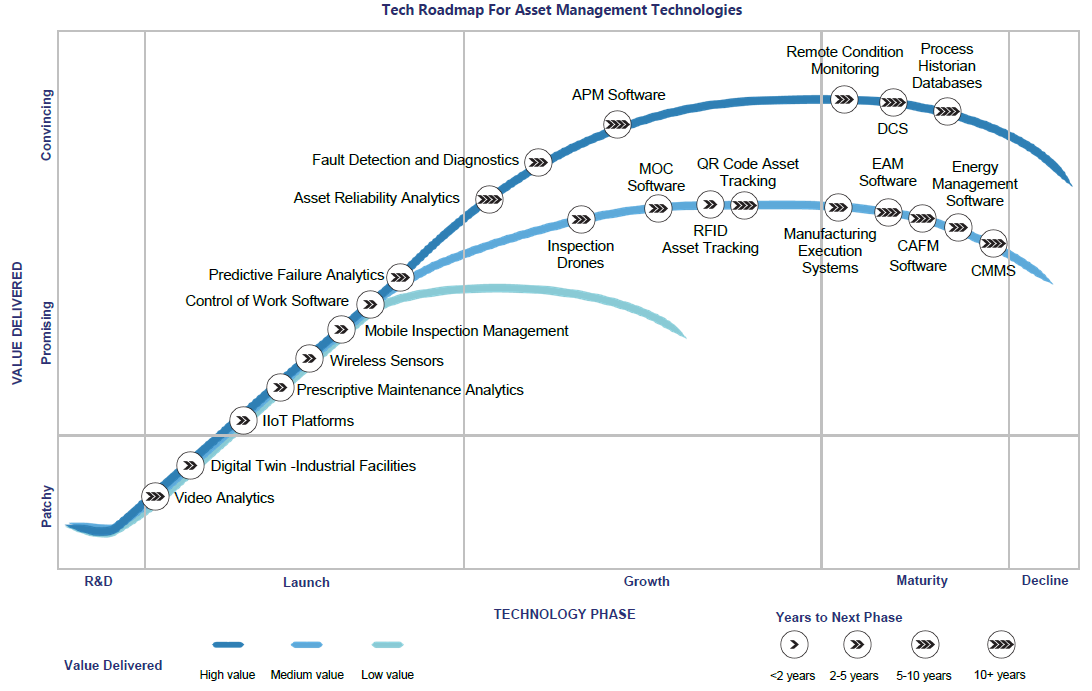
As competition increases, manufacturers are under pressure to reduce costs and risks, improve customer experience and increase profitability. Those armed with digital forces are disrupting business models with new value propositions. These disruptions cause a challenge for manufacturing organisations who should seriously consider the benefits of adopting digital technologies themselves.
Digital technologies
Digital technology presents some immediate advantages that can help discover inefficiencies and keep maintenance costs low, such as:
- Manage backlogs | By delaying preventive maintenance, more money will be spent on repairs. The use of technology allows for greater visibility of problems and tasks to be performed, making backlogs difficult to ignore and reducing the number of unresolved work orders.
- Fault finding efficiently | Repairing or replacing an asset without a database of information about the equipment in question can be a nightmare. A digital platform allows the maintenance team to analyse detailed data to discover which assets need to be repaired and how and when it is most cost-effective to invest in new equipment.
- Predictive/prescriptive maintenance | The digital transformation allows companies to design maintenance processes in a much more efficient way.
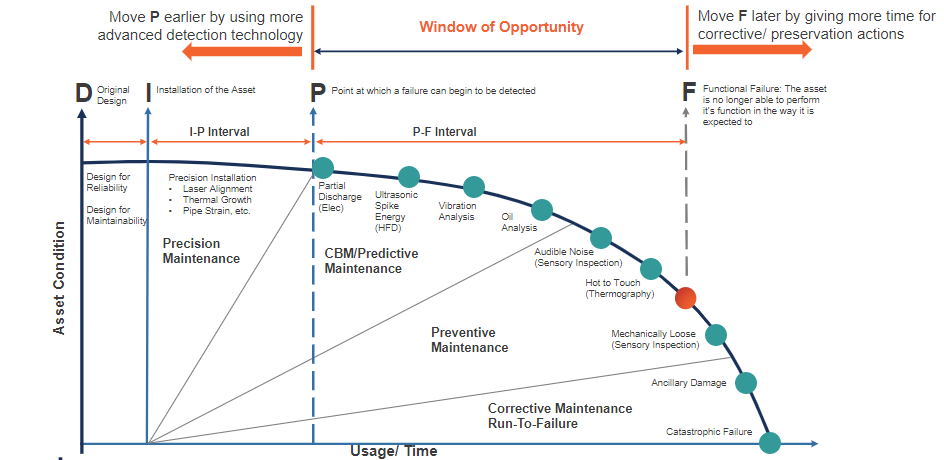
- Remote work | Remote maintenance consists of carrying out some operations in remote locations. The service personnel on-site transmit all the relevant information to the support desk or the planning office, speeding up problem solutions and reducing travel costs.
Common technologies
There are quite a few digital transformation technologies out there, but we find the ones listed below are more common and easily implemented in manufacturing companies.
Real-time Analytics | Big Data is various structured and unstructured large-volume data and its processing methods that allow analysing information in a distributed manner. When transitioning to new technological systems, the amount of data received exponentially grows. It needs correct processing to generate reports that would allow making management decisions in the promptest way possible. In the context of asset management, the ability to get reports in real-time and the ability to organise collaboration is a significant advantage.
Application Programming Interface (API) | Various technological solutions based on API and integrated into the EAMS software used at the company facilities are a simple and affordable way to use machine learning capabilities and several other technologies. This approach allows companies to create a complete platform for promptly solving important asset management tasks and with small budget investments is a powerful and flexible tool used to integrate different components into a single system.
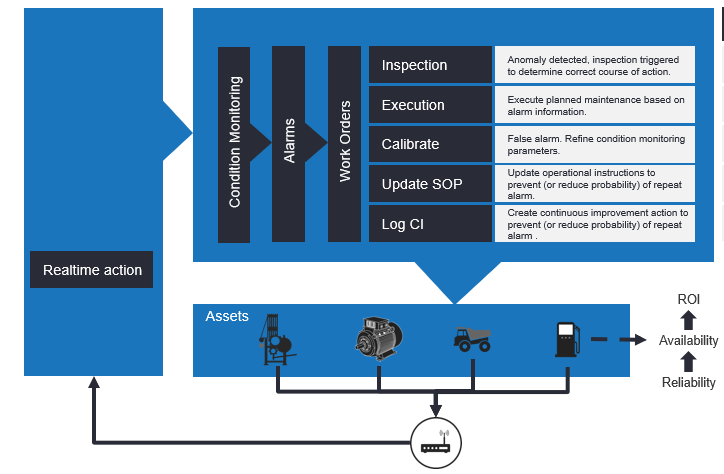
Cloud Technology | Cloud technologies are capable to fundamentally change existing business models. Their utilisation provides the ability to flexibly use remote resources with the purpose of storing and processing data on demand, and that substantially reduces hardware and infrastructure costs. This tool ensures efficient work of teams online and allows storing large amounts of data, as well as maintaining their security at the highest level. Another important advantage of using cloud technologies is the economic benefit for businesses. After all, in-house hardware purchase proves more profitable only for the following few years after the purchase.
Mobility | Mobile applications bring adaptability and portability to businesses. Today, remote working is thriving, and flexibility in work schedules is more common – this environment makes mobile a powerful technology that will help people stay connected with a finger touch. Mobile is also a powerful technology that is a basic necessity for many other technologies like AR, IoT, etc. Mobile enables people to work on the move, gives them more control, and improves their operations. It facilitates real-time communication, which is great in industries like manufacturing. The portability offered by mobile devices empowers people to perform tasks, coordinate, and communicate, even when on-field.
People
It’s evident that as technology takes over much of repetitive work, many traditional manufacturing jobs will phase out. Also, with an increased supply chain demand, companies are automating operations to speed up production.
Humans will remain at the heart of the manufacturing industry. But, as the scope of their jobs shifts away from traditional hands-on manufacturing, workers will need to develop new skills. Jobs such as data analysts, software engineers, programming for IoT, robotics and automation, customer service, research and development, product development and sales and marketing will be the in-demand jobs for this era.
Digital transformation should promote a cultural change that will also affect the technical staff, providing them with knowledge and technical skills essential for improving their areas of expertise.
This change in mentality promotes a more open company, sharing information transversally from the bottom up. This change helps asset managers better understand the implications of their activity and have useful information for planning and actioning maintenance more efficiently, in line with its objectives.
Digital transformation objectives
It is also important to define the measurable objectives that will be used to guide digital transformation within the company. Questions should be asked such as:
- What are the pain points/opportunities and gaps between where we are and where we want to be in terms of asset management?
- What technologies or solutions are out there that can be used in asset management?
- What does our ideal state or our “digital dream” look like?
- How do we get there?
- Who needs to be empowered?
In closing, to embrace new technologies, a company needs to develop a digital strategy and choose the best solution for its asset management strategy and digital journey. This journey needs support from its executives, as well as the establishment of cross-functional teams. To remain competitive, asset managers need to know how these transformations will affect and potentially improve how their company manages their assets.
However, beyond the direct advantages of using technology, we must bear in mind that digital transformation is a process of change that involves the whole company and allows the use of technology to be integrated into the company’s overall strategy. This transformation affects both the organisation and people as well as processes and must be applied in all areas, including the management and maintenance of physical assets.